Разработка уральских ученых позволит сэкономить металлургам 8 миллиардов рублей
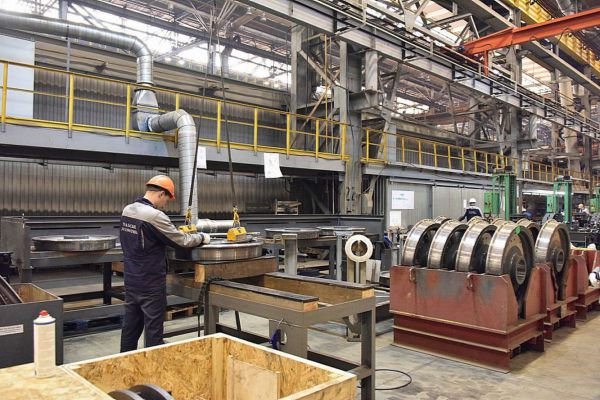
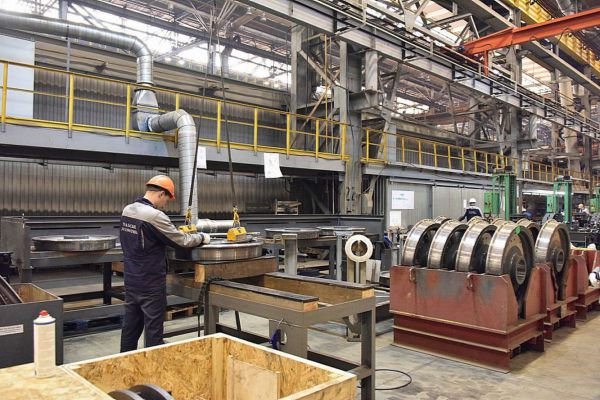
Речь идет об очень стойком покрытии деталей, которые используются при плавлении стали. По словам члена-корреспондента РАН, главного ученого секретаря УрО РАН, заведующего отделом материаловедения и лабораторией механических свойств Института физики металлов УрО РАН Алексея Макарова, в металлургии крайне важны материалы, способные выдерживать высокие температуры. Чаще всего, чтобы достичь нужного эффекта, составы покрытия комбинируются и создаются композиционные материалы.
– Мы же обнаружили новый способ повышения стойкости. В ходе экспериментов нам удалось выявить эффект, при котором нагрев покрытия при температуре свыше 1000 °C приводит не к ослаблению его свойств, как при 800 °C, а наоборот к упрочнению. Таким образом, покрытие переходит в разряд жаропрочных, и это значительно расширяет возможности его применения. Анализ природы этого эффекта мы уже опубликовали в научных журналах, а сама технология нашла применение на научно-производственном предприятии «Машпром», – говорит Алексей Макаров.
В частности, технология используется в кристаллизаторе машин непрерывного литья заготовок – это специальное металлургическое оборудование, с помощью которого сталь разливается по формам.
Как отметил Алексей Макаров, разработкой заинтересовались не только российские предприятия, но и китайские. Поднебесная считается лидером в производстве стали, и изготавливает в 10 раз больше, чем российские или американские заводы, но даже там о подобной технологии не знали.
– До этого на российских предприятиях использовались импортные комплектующие, – говорит руководитель проекта «НПП «Машпром» Александр Вопнерук. – И изначально к нам обратились из ЕВРАЗ НТМК с просьбой сделать кристаллизаторы машин, не уступающие зарубежным. В Институте физики металлов УрО РАН началась работа, и в итоге, была разработана технология, получившая большой отклик. Кроме того что она позволяет значительно увеличить объемы производства, технология помогает предприятиям сэкономить на ремонте и обслуживания оборудования порядка 7-8 миллиардов рублей. Также разработка была внесена в федеральный реестр новых технологий. Но одно из главных достижений этой работы в том, что теперь при строительстве новых комплексов ЕВРАЗ уже просит учитывать, что на предприятии будет использоваться именно технология Института физики металлов УрО РАН.
Еще одна работа, в которой приняли участие ученые Уральского отделения Российской академии наук, связана с высокотемпературной гальванопластикой – производством изделий с помощью электрического тока.
– Это технология позволяет создавать новые материалы, способные выдерживать температуру до 200 °C в окислительной среде. В первую очередь, это востребовано при производстве двигателей, в том числе, для космической отрасли. Сегодня эту технологию мы уже внедряем на территории материаловедческого предприятия «Композит» Госкорпорации «Роскосмос», – говорит заведующий лабораторией электрокристаллизации и высокотемпературной гальванотехники Института высокотемпературной электрохимии УрО РАН Андрей Исаков.
Глава отдела металлов и металлургических технологий АО «Композит» ГК «Роскосмос» Валентин Каширцев отмечает, что в Москве таких специалистов как в Екатеринбурге нет, поэтому все научное руководство над процессом было доверено уральским ученым.
Более того, до прошлого года в «Роскомосе» работа в сфере высокотемпературной гальванопластики даже не велась.
– Решение о создании с нуля производства, где бы использовался метод гальванопластики, было принято в 2018 году и 2020 году началось его формирование. Это новая технология, не похожая на классическую металлургию, и не все готовы ее воспринимать. Но только она, на сегодняшний день, позволяет качественно, с учетом всех нормативов работать с драгметаллами, создавать камеры сгорания двигателей для спутниковых систем, и даже создавать многоразовые двигатели, – заключает Валентин Каширцев.